Why should companies invest in industrial automation during the times of pandemics?
How can automation help your company in times of outbreak?
Robots = less production vulnerability
Industrial automation can help drastically improve the resistance to pandemics and similiar crisis of your company. The developments of the last few weeks have clearly shown how the current, globally interconnected, economy is sensitive to any issue. Production vulnerability stems foremost from the dependency on two major factors:
- the continuity of supplies from places away from the final production site,
- sensitivity to the workforce movement.
The use of collaborative robotics can significantly reduce the influence of these two factors. Robotization allows your production to stay local and decreases your company’s dependency on workforce mobility.
Introduction of massive collaborative robot use
Production was originally moving to regions with lower workforce costs due to economic reasons. However, this process is being drastically reduced by the introduction of robotics. The costs of a robotic workspace are roughly the same everywhere on the planet. Measured by the recent development a question arises: Is it efficient to save few euro-cents per part and subsequently lose millions of Euro caused by necessary production down-times due to a lack of parts and the limited workforce mobility?
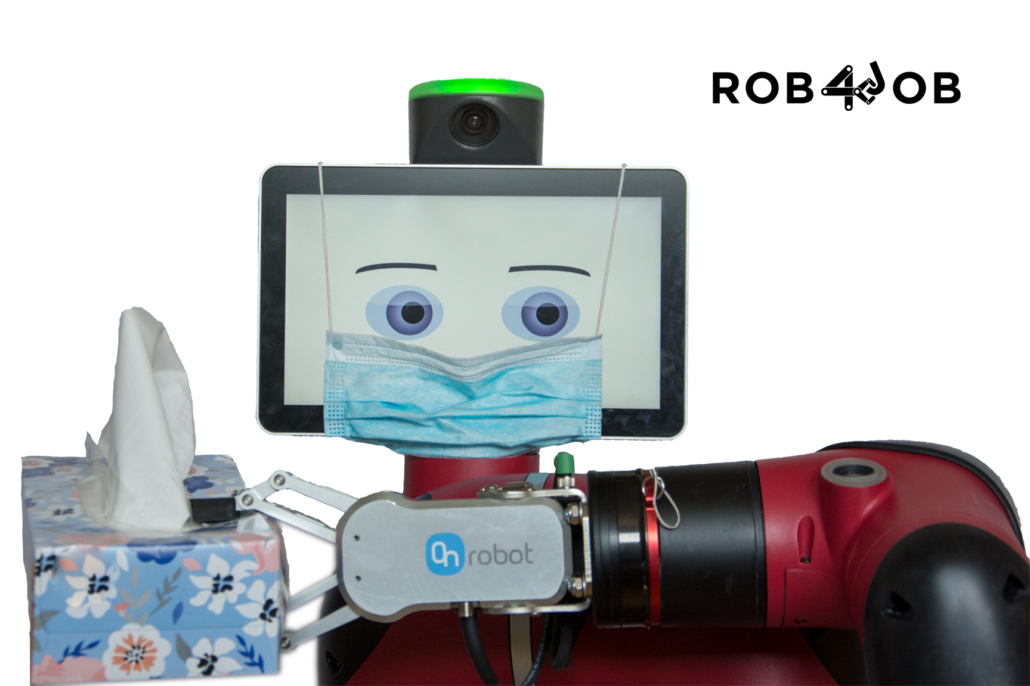
How can robotics help in the times of the pandemic?
1. More robust value chain
Industrial automation leeds to keeping most of the production local, in the main focus area of the company, you can substantially lower the impact risk of the main problems like pandemics, risks stemming from ecological activities (such as long-haul travel restrictions), civil unrest, trade restrictions, wars etc… Robots allow you to make the most of the on-shoring trend, moving the production back to the region were the R&D and product development is located.
2. Reaction and communication speed
Lowering the geographical distance between individual production chain links leads to improved speed of reaction between them. That applies to development of new products, problem management, product modification and adjustments according to the customer’s needs. The lesson learned from the Boeing crisis proves that its always cheaper to keep production, software development, testing, R&D, and the economical parts of the company close together.
3. Faster and better work-force development
Implementing collaborative robots drastically changes the needs of work force qualifications. Instead of an “object manipulator” (a human performing a pick and place job) the companies implementing cobots need skills like robot operator.
If a company neglects this new trend it is going to face serius issues with the structure and skill set of the workforce within a couple years. Moving the production lines to remote sites is not going to help developing the skill set of the local workforce.
Individual topics will be discussed in upcoming short texts.
And a last side note: a robot does not have to be quarantined.